Architectural color coating board, coating options
The material requirements of buildings (roof panels and exterior wall panels) themselves can be divided into safety performance (impact, wind pressure and fire resistance), residential performance (water resistance, heat insulation and sound insulation), durability (pollution resistance, weather resistance) and manufacturability (economy, easy to work with, easy to maintain and repair).
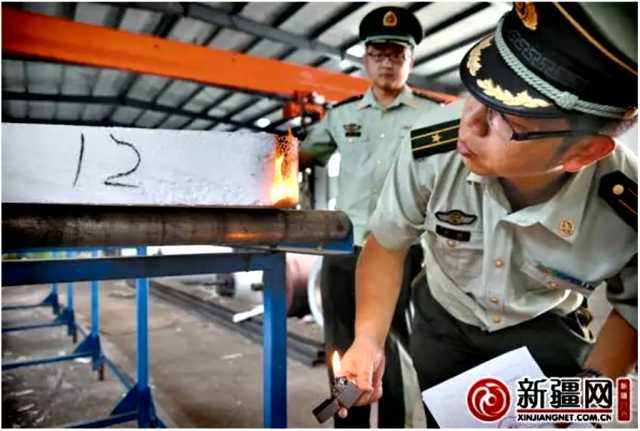
Safety and service life are of Paramount importance to the ultimate owner of the building.For the design unit, the service life, bearing capacity, appearance, more important.And for the building wall and roof processors, color coated board processing (surface hardness, wear resistance, plate shape and steel strength) is the preferred requirements.
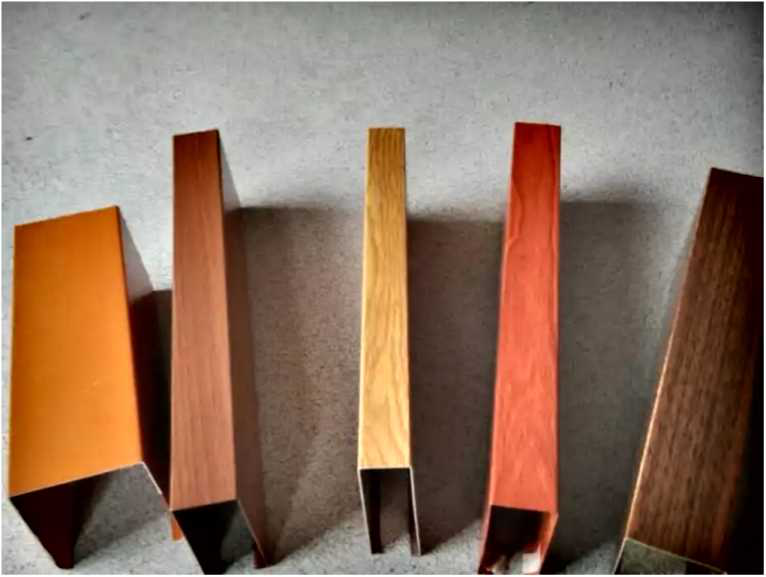
Of course, the quality of the color coated board mainly depends on the color coated board manufacturer, but if the processing and installation equipment and methods are not appropriate, will also cause different degrees of damage to the appearance of the final product and service life.
The performance of color coated board mainly includes:
Substrate: yield strength, tensile strength, elongation
Coating: coating weight, binding force
Coating: chromatic aberration, gloss, t-bend, impact, hardness, powder resistance, moisture and heat resistance, etc
Surface: visible surface defects, etc
Plate type: tolerances, irregularity, etc
1 The steel grade
For buildings, the bearing capacity (wind load, snow load, construction personnel thick wood), the span of the building, etc., depends on the hardness of the steel plate, for the building maintenance structure with color coating and aluminum zinc plate, there are corresponding standards at home and abroad.For example, Chinese GB/T 12754-2006, American astm653.a STM792, Japanese JISG3302, JISG3321, European en10215.en10147, etc.It is divided into CQ (ordinary commercial grade), D Q (general stamping), HSS (high strength structural steel) and FH (full hard steel).
CQ
Now the most commonly used, such as baosteel produced by the TDC51 class SU, yield strength between 260-320MPa, tensile strength between 350-400MPa, relative to the structural steel, its flexion ratio is slightly higher.
DQ
Due to the general construction color board are roller forming or composite sandwich, the requirements for the stamping performance of materials is not high, so the DQ class is mainly used in doors, Windows, pipelines and other industries.
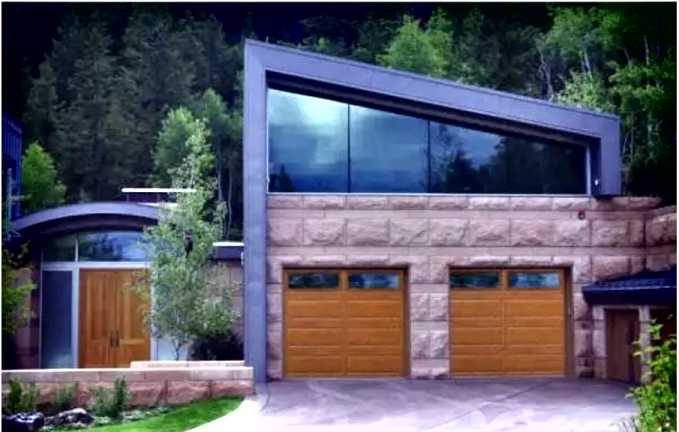
HSS
High strength structural steel: according to European standard HSS, it can be divided into 4-5 kinds of steel with different strength. However, since ordinary CQ grade materials have been able to replace low-strength HSS steel, the steel with yield strength of 280MPa and 345MPa are widely used in the market. The TS280GD and TS350GD produced by baosteel are these two steel types.
Compared with CQ, HSS steel has several advantages:
1) as the flexion strength is relatively low, the steel has good fire resistance and shock resistance.
2) for thicker steel plates, it can be used to manufacture large-span arch plates.
3) for general external walls and roof panels, it can be thinner than CQ materials, thus saving material consumption.
FH
Full hard steel: it is a kind of steel that can improve the yield strength of steel plate by controlling annealing temperature. According to the international general standard, the yield strength is greater than 550MPa, the tensile strength is greater than 570MPa.
2 Selection of coating
Coating is to ensure the durability of the building, corrosion resistance and consideration, different USES can be selected by different coating, coating and thickness to meet its service life.
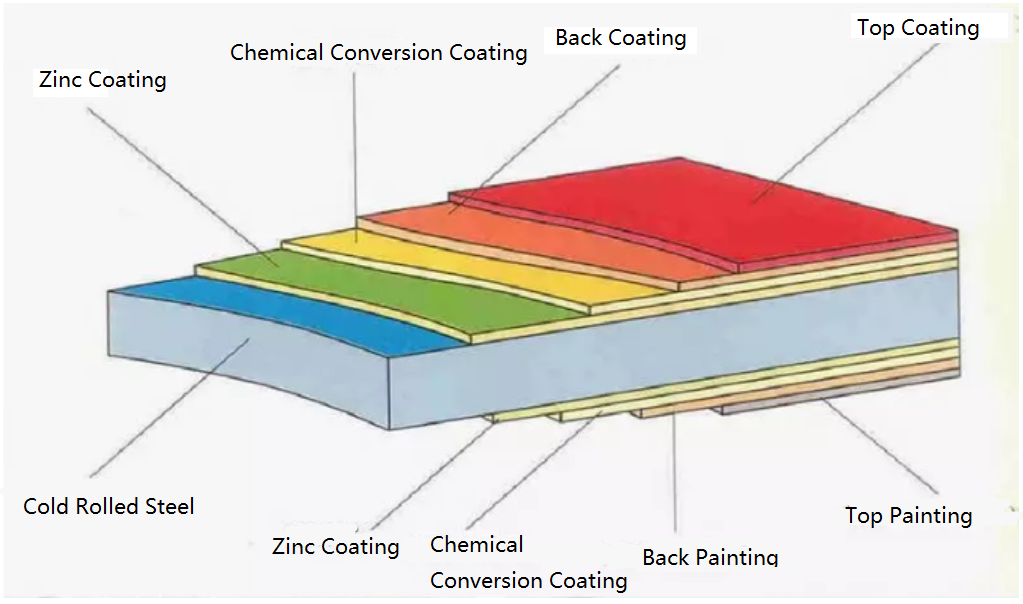
2.1 The plating
Construction with color coating now common coating for hot – dip galvanized and hot – dip aluminum zinc two kinds.For color coating, there is little difference between the two substrates. In the relatively acidic environment, aluminum-zinc substrates are a better choice.For wet, alkaline environment, the use of galvanized substrate notch corrosion resistance to reflect the advantages.
For coating thickness, on the roof panel and cladding the general requirements for hot dip galvanized is greater than 80 g/m2 (about 26 microns), aluminum zinc plating is greater than 100 g/m2 (about 27 microns), when using the environment in heavy industry or the beach, foreign related association has a minimum amount of galvanized, such as ECCA specification and Australian standard requirements zinc plating layer weight greater than 275 g/m2 (about 38 microns), aluminum zinc plating is greater than 150 g/m2 (about 40 microns).
Hot aluminized zinc substrate has excellent corrosion resistance and is suitable for the production of building panels.
Hot dip galvanized substrate has excellent corrosion resistance. It is suitable for making building exterior panels, and can be processed in general forming, stamping, deep stamping and other levels.
Electroplated zinc substrate has good corrosion resistance, thin zinc coating and good processing performance. Suitable for making household appliances, steel Windows or indoor saitama etc.
2.2 The coating
Must satisfy the user to the color demand and the durability request.For processors to meet its processing performance.So in order to explain the type of paint, color and gloss, coating thickness.
Now commonly used coil steel coating topcoat varieties are polyester (PE), polyurethane (PU), silicon modified polyester (SMP), fluorocarbon (PVDF), high weathering polyester (HDP), primer and back paint varieties are epoxy (EP), polyester (PE), polyurethane (PU) and so on.
The choice of color is mainly to consider the matching with the surrounding environment and the owner’s hobby, but from the perspective of the use of technology to say that the light color heat reflection ability is strong, coating film powder after the contrast is small, if cleaning and maintenance is appropriate, the service life will be long, will be more beautiful.
For the gloss, in the outdoor use of color coated board, the loss of light occurred the earliest phenomenon, especially the high gloss product its initial loss of light quickly.In glossiness falls to 20 or so can maintain relatively long time, this kind of phenomenon can appear in use a few months, accordingly, outdoor building USES colour to besmear board is low light commonly.
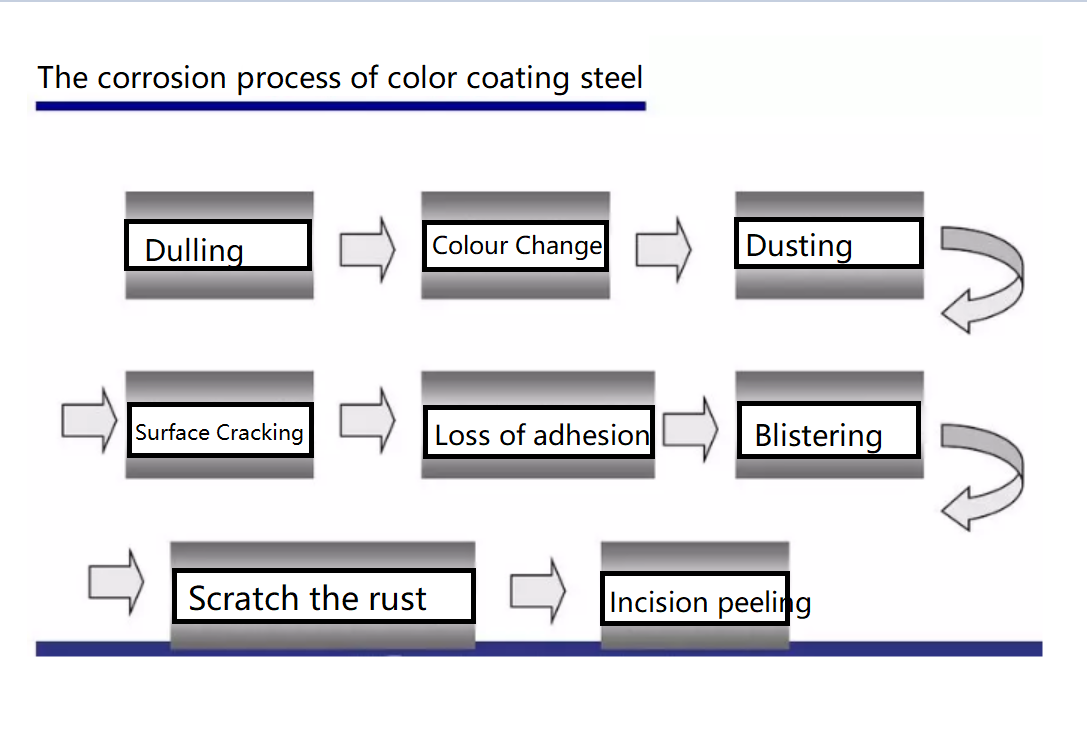
In addition, in the same building should use the same color coating factory produced products.Because different manufacturers of painted steel plate in the outdoor use of a certain number of years after the coating powder speed is different, even if the building seems to be the same, after a period of time will appear different colors of the visual effect and affect the beauty.
Microscopically, coatings are porous tissues.Water in the air and corrosive media (chloride ions, etc.) will invade through the weak part of the coating, causing submembrane corrosion, which causes the coating to bubble and flake.In addition, secondary coatings are denser than primary coatings, even with the same coating thickness.
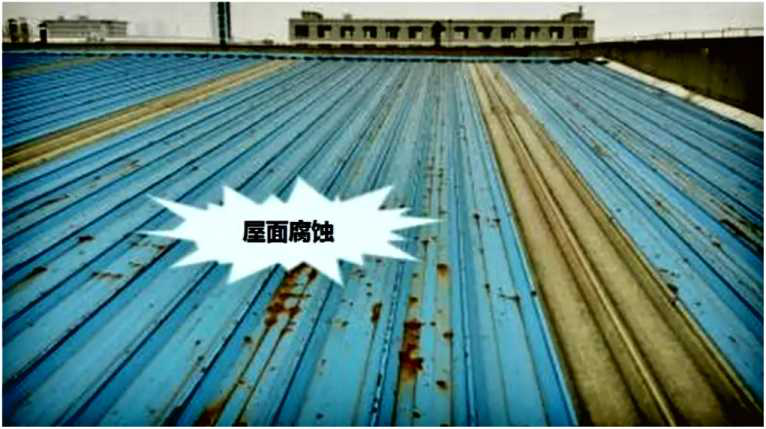
According to the relevant corrosion test results, the front coating of more than 20 microns to effectively prevent the invasion of corrosive medium.PVDF products require a thicker film.Requirements for the back coating depend on the use, sandwich plate only requires a layer of adhesive primer, and formed steel plate due to indoor corrosion environment so also requires two layers, thickness of at least 10 microns.